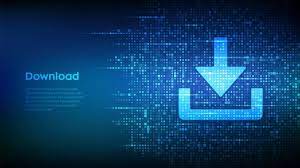

Well maintained conveyor systems can reliably operate at 90% or higher availability.Belt replacement is on average every 5 years for hard rock applications and up to 15 years for non-abrasive applications.

#THE POWER HOUR 911 PLUS#
Estimated operating maintenance cost per year for a belt conveyor is 2% of the purchase cost plus 5% of the belt cost.Beyond 1 km distance, the ton-mile cost of transport by belt conveyor may be as low as 1/10th cost by haul truck.CEMA agrees with the second bullet point above and adds four other economic points. A further attempt to provide guidelines for the selection of forms of haulage on cost grounds can be found in the Conveyor Equipment Manufacturers Association (CEMA) publication.As a rule, belt conveyor operation is more economical than truck haulage if the conveying distance exceeds I km.An underground mine is more economically served by a belt conveyor than railcars or trucks when the daily mine production exceeds 5000 tons.The ‘Rules of Thumb’ set out by McIntosh Engineering underline the advantage of belt conveying across the spectrum of operations. However, over the years the capacity rating of belt systems and the length over which material can be transported have increased very considerably, together with the power inputs, the size of components, and the degree of sophistication. The idea of using the conveyor belt is not new, indeed, the first bell conveyors were introduced at the end of the nineteenth century the basic principles of operation have not changed. Belt conveyors used to transport minerals are to be found all around the world in a large number of surface and underground mining operations.
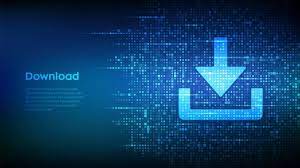